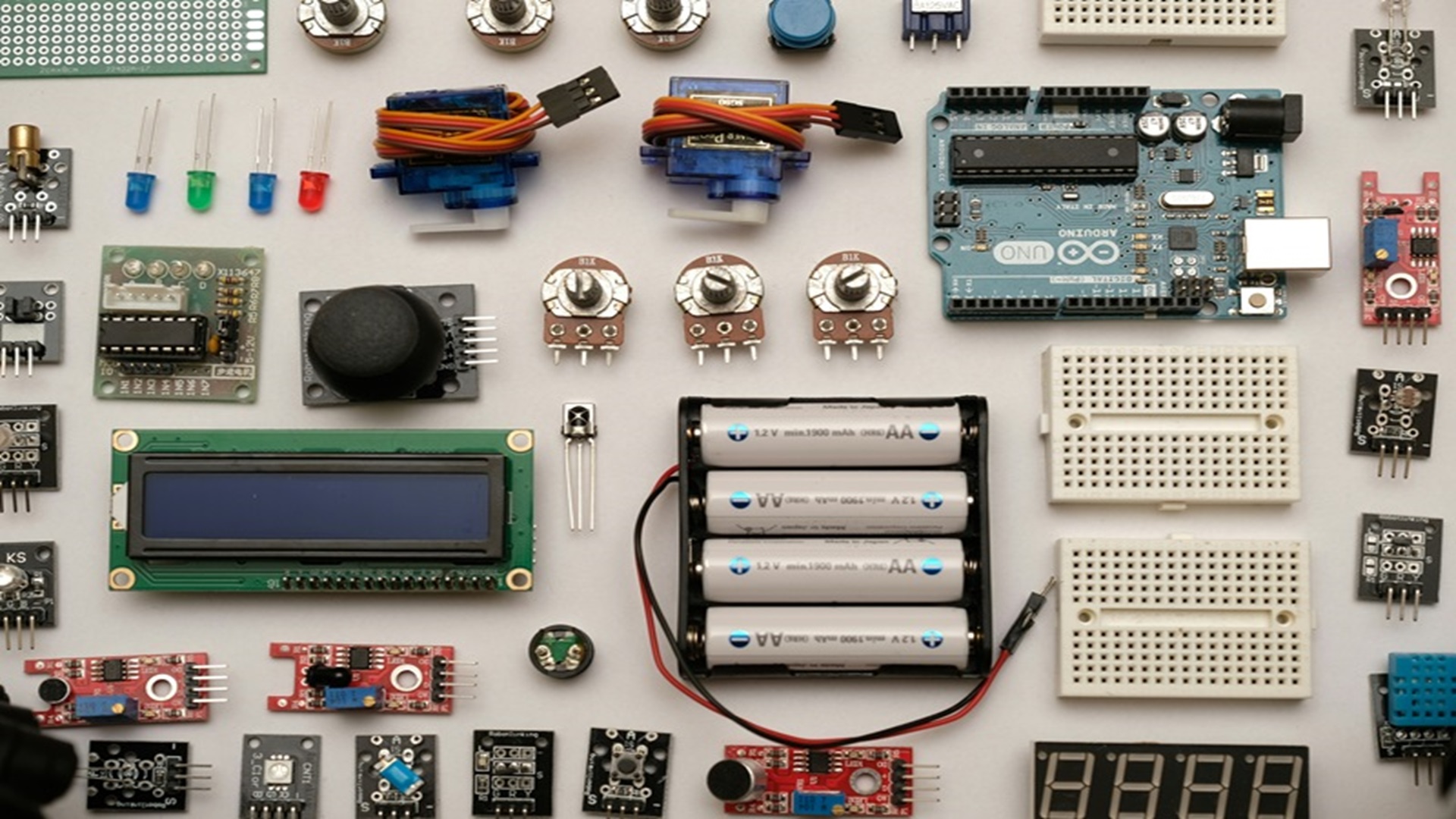
Whether you’re packaging lithium-ion cells, rechargeable batteries, or specialized power solutions, custom battery packaging serves as your first line of defense and a powerful marketing tool. This comprehensive guide walks through creating safe, compliant, and brand-enhancing battery packaging.
Products from this article
Why Custom Battery Packaging Matters
- Safety Compliance – Meets UN/DOT 38.3 testing requirements
- Brand Differentiation – Stand out in competitive energy markets
- Technical Specifications – Tailored to battery dimensions and chemistry
- Sustainability – Meets growing demand for eco-conscious solutions
- Retail Readiness – Ready-to-shelf designs for consumer electronics
7-Step Process for Custom Battery Packaging Design
1. Define Technical Requirements
- Battery type (Li-ion, NiMH, Alkaline)
- Dimensions and weight specifications
- Stacking/transportation needs
- Child-resistant features (CPSC compliance)
- Environmental factors (moisture/static protection)
Pro Tip: Include a 3D model of your battery for precise fit engineering
2. Material Selection Guide
Material Type | Best For | Certifications |
---|---|---|
Corrugated Fiberboard | Consumer AA/AAA | FSC Certified |
Static-Shielding Bags | Industrial Batteries | ESD S20.20 |
Thermoformed Blisters | Retail Displays | UL 94 V-0 |
Poly Laminate Pouches | Rechargeable Packs | UN 38.3 Certified |
3. Safety & Compliance Engineering
- Integrate mandatory warnings (Caution/CR17345 labels)
- Pressure relief vents for Li-ion cells
- Ingress Protection (IP) ratings as needed
- Include multilingual safety instructions
4. Branding & Visual Design
- High-contrast warning zones vs brand messaging areas
- Battery performance infographics
- QR codes linking to spec sheets/safety videos
- Embossed logos for tactile branding
5. Prototyping & Testing
- Conduct real-world simulations:
- Vibration testing (ASTM D4728)
- Drop testing (ISTA 3A)
- Climate chamber testing
- Verify child-resistant features
- Check for EMI/RFI interference
6. Sustainability Integration
- Incorporate recycled PET materials
- Design for disassembly (separate material streams)
- Add battery recycling instructions
- Consider plant-based bio-barrier films
7. Production & Quality Assurance
- Implement inline conductivity testing
- Batch traceability systems
- Automated vision inspection for labeling
- Final compliance audit before shipping
Top 5 Custom Battery Manufacturers in China

Specialization: Lead-acid, gel, and lithium-ion batteries
Key Features:
- Customizable voltage configurations (24V, 48V, 96V+) for solar, UPS, and telecom systems.
- Compliant with UN/DOT safety standards and IP-rated designs for harsh environments.
- Offers wall-mounted and rack-mounted battery solutions with LCD monitoring systems.
Why Choose Them: Over a decade of experience, FSC-certified materials, and a 20,000 sqm production facility in Jiangsu Province.
Specialization: Lithium iron phosphate (LiFePO4) batteries
Key Features:
- UL1973, UN38.3, and IEC62619-certified batteries for solar storage, marine, and industrial use.
- Customizable modular designs with intelligent battery management systems (BMS).
- Annual production capacity of 3GWh, serving Fortune 500 companies and 80,000+ households globally.
Why Choose Them: Cutting-edge automation, eco-friendly LiFePO4 technology, and partnerships with leading solar retailers.
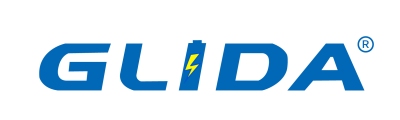
Specialization: Wholesale lead-acid, lithium-ion, and NiCd batteries
Key Features:
- Bulk orders with MOQs as low as 1–100 units and competitive pricing (7.9–1,136/unit).
- Supports OEM/ODM services for custom voltage, capacity, and form factors.
- Compliant with CE, RoHS, and ISO certifications.
Why Choose Them: Streamlined supply chain, fast dispatch, and verified supplier credentials on Made-in-China.
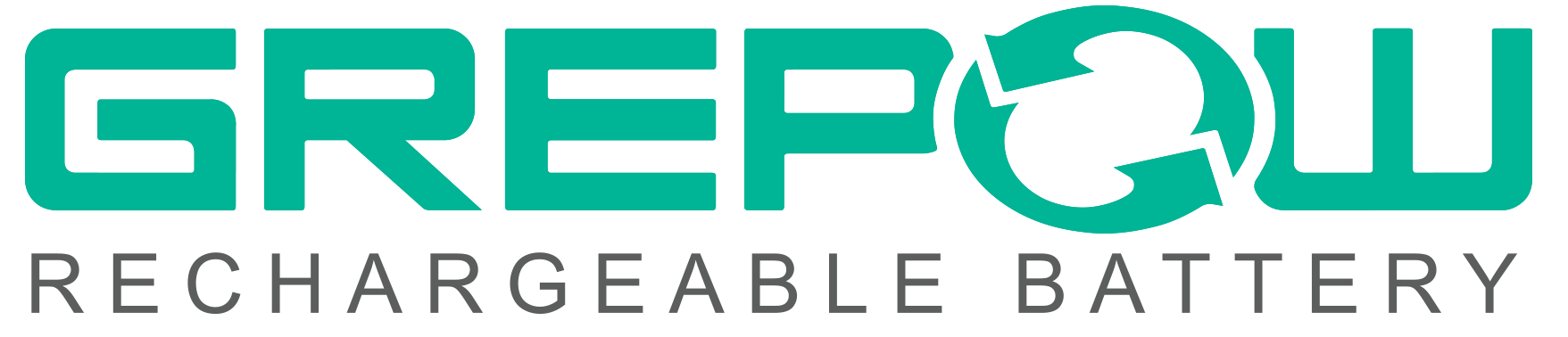
Specialization: Li-ion and LiPo batteries for mobile devices
Key Features:
- Custom capacities (1,000–10,000 mAh) and sizes for smartphones and IoT devices.
- MOQs from 10–10,000 units, priced at 0.03–24.5/unit.
- Anti-leakage and overcharge protection technologies.
Why Choose Them: Rapid prototyping, water-soluble coatings, and QR code traceability for quality assurance.
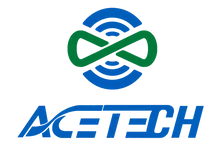
Specialization: Advanced lithium-ion and lead-acid storage solutions
Key Features:
- Customizable high-voltage packs (up to 384V) for industrial and renewable energy systems.
- Climate-resistant designs tested under ASTM D4728 and ISTA 3A standards.
- Supports low MOQs (50+ units) and eco-friendly materials like recycled PET.
Why Choose Them: Expertise in bespoke energy storage systems and compliance with FCC/UKCA regulations.
FAQs
Q: How much does custom battery packaging cost?
A: Costs vary based on materials (0.25−5/unit), MOQs (typically 5,000+ units), and certifications needed. Request a quote with your specs.
Q: What’s the minimum order quantity for custom designs?
A: Most manufacturers require 5,000-10,000 units for custom battery packaging solutions.
Q: How long does custom battery packaging development take?
A: Allow 8-12 weeks including design, testing, and production (expedited options available).
Q: Are there eco-friendly options for battery packaging?
A: Yes! Explore PCR plastics, mushroom-based cushioning, and water-soluble anti-static coatings.
Q: What certifications should battery packaging have?
A: Look for UN 38.3, UL 2054, IEC 62133, and country-specific compliance (FCC, CE, UKCA).
Q: What certifications should I check when sourcing custom batteries?
A: Look for UN38.3, UL1973, CE, and RoHS compliance.
Q: Can I order small quantities for prototyping?
A: Yes—many manufacturers accept MOQs as low as 10–50 units.
Q: How do I verify a supplier’s reliability?
A: Request samples, audit factories virtually, and confirm certifications via platforms like Made-in-China.